One of the newest tech trends today is flexible electronics. Especially those with different form factors. Many of which would require a flexible circuit board. Foldable phones, for example, are the newest trends in gadgets. Along with smart watches, curved or flexible displays and speakers. Even now the continuous quest to create thinner and thinner laptops and phones require the creation of the best flexible circuit board. Devices that should be able to withstand the stresses of extensive daily use.
As opposed to regular rigid circuit boards or PCBs the flexible circuit board (FPCB), is very thin, lightweight and flexible. They are often made of clear cellophane-like material such as copper-coated polyimide. This enables electronics manufacturers to create smaller, thinner, more flexible devices like mobile phones, wearables and ultrabooks. Their flexibility allows manufacturers to easily create smaller electronics of various shapes which were not possible decades ago. The flexible circuit board also allows for more complexity in circuit paths by easily allowing more layers while maintaining a thin profile. Flex boards can have from one to four layers depending on the complexity of the device.
Advantages of flexible circuit board
- Other than their thinness and lightweight, design constraints are now minimal. Devices of various shapes can now be made because of the softness and flexibility of FPCBs.
- With flexibility, FPCBs also allow for a wider range of motion, making it suitable for any application. Their flexibility and lack of mass also makes them less susceptible to vibrations.
- FPCBs are also less susceptible to bending allowing for millions of flex cycles compared to ribbon cables.
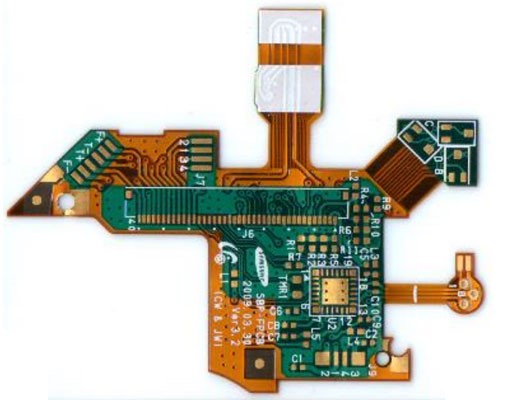
Creation of Flexible Circuit Boards
Creation of a flexible circuit board involves the same processes as that of a rigid PCB. The flexible board can be purchased from electronics shops and with the right equipment such as a wax-based inkjet printer to print circuit patterns, FPCBs can be easily created right at home for prototyping and proof of concept. Once refined, the design can then be submitted to one of dozens of PCB fabrication companies for manufacture.
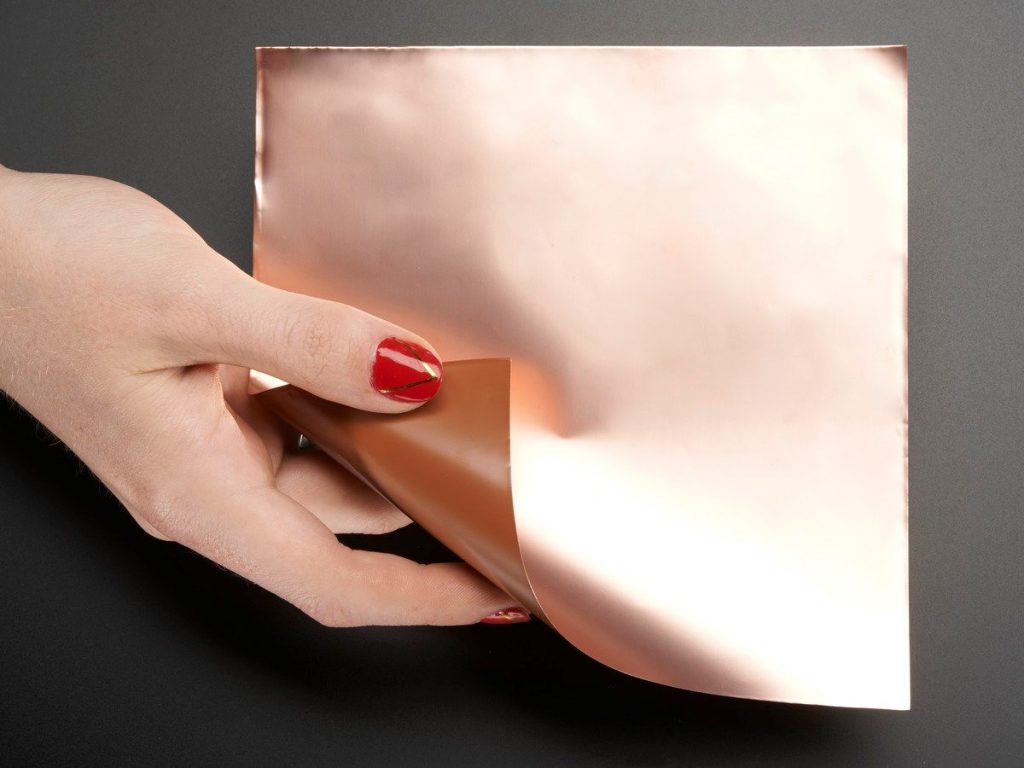
There are several types of flexible PCBs available depending on the application.
- There’s the single-sided circuit with only one layer of conductor on a flexible dielectric film. This is the simplest and least expensive to produce.
- Then there’s the double-sided circuit where both sides of the dielectric film are used which doubles the electronics or circuits of a given area.
- The most complex would be the multi-layer circuit where several layers of circuitry are made on multiple layers of conductor and film. The conductor layers are connected by holes between the layers.
- FPCBs can also be designed and used in conjunction with rigid PCBs which results in rigid-flex or Type 4 circuits
- And lastly, sculptured flexible circuits where the thickness of the conductors vary across the circuit with the purpose of a circuit having both flexibility and structural strength in various sections.

The best flexible circuit board of course are ones that are optimally designed and produced with the lowest cost. Many fabricators also include design services that not only reduces costs for the customer but reduces their production costs as well while resulting in often improved and optimal designs.